Aluminum Alloy Ingots

The characteristics of the aluminum alloy ingots used for die casting processes are demonstrated as below tables.
Most commonly used is ADC12 which is also known as A383. It is commonly used for die casting applications and is a cost-effective and easy-to-work-with material that offers good mechanical properties and dimensional stability. ADC12 is a modified version of the ADC10 alloy, and it has slightly lower strength but better fluidity. This makes it a good choice for complex die-casting projects.
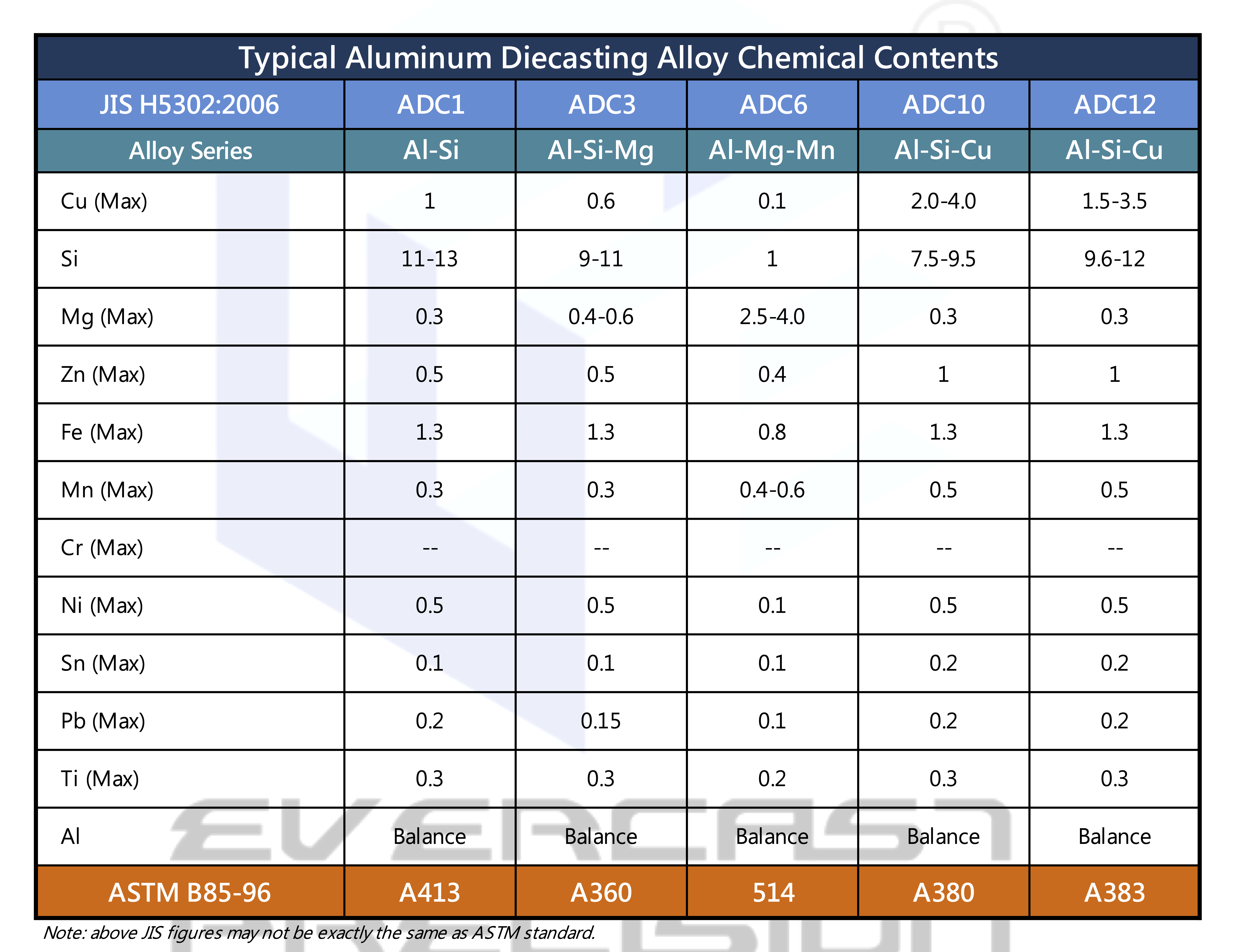

As you can see, ADC1 has the lowest tensile strength and yield strength of the four alloys. However, it is also the lowest cost alloy. ADC10 has the highest tensile strength and yield strength of the four alloys, but it is also the most expensive. ADC12 has a tensile strength and yield strength that is in between ADC3 and ADC10. ADC1 has a tensile strength and yield strength that is slightly lower than ADC3.
In terms of other properties, ADC1, ADC3, ADC10, and ADC12 are all similar. They have good corrosion resistance, dimensional stability, and machinability. ADC1 is the least weldable of the four alloys, but it is still weldable with some difficulty.
Overall, the best choice of alloy will depend on the specific application requirements. If cost is a major factor, then ADC1 is a good option. If high strength is required, then ADC10 or ADC12 may be a better choice. ADC1 is a good choice for applications where low cost and good machinability are important, such as electrical appliances, household utensils, and toys.